Platinum TSS200 Handleiding
Bekijk gratis de handleiding van Platinum TSS200 (11 pagina’s), behorend tot de categorie Kabels voor pc's en randapparatuur. Deze gids werd als nuttig beoordeeld door 77 mensen en kreeg gemiddeld 4.0 sterren uit 39 reviews. Heb je een vraag over Platinum TSS200 of wil je andere gebruikers van dit product iets vragen? Stel een vraag
Pagina 1/11
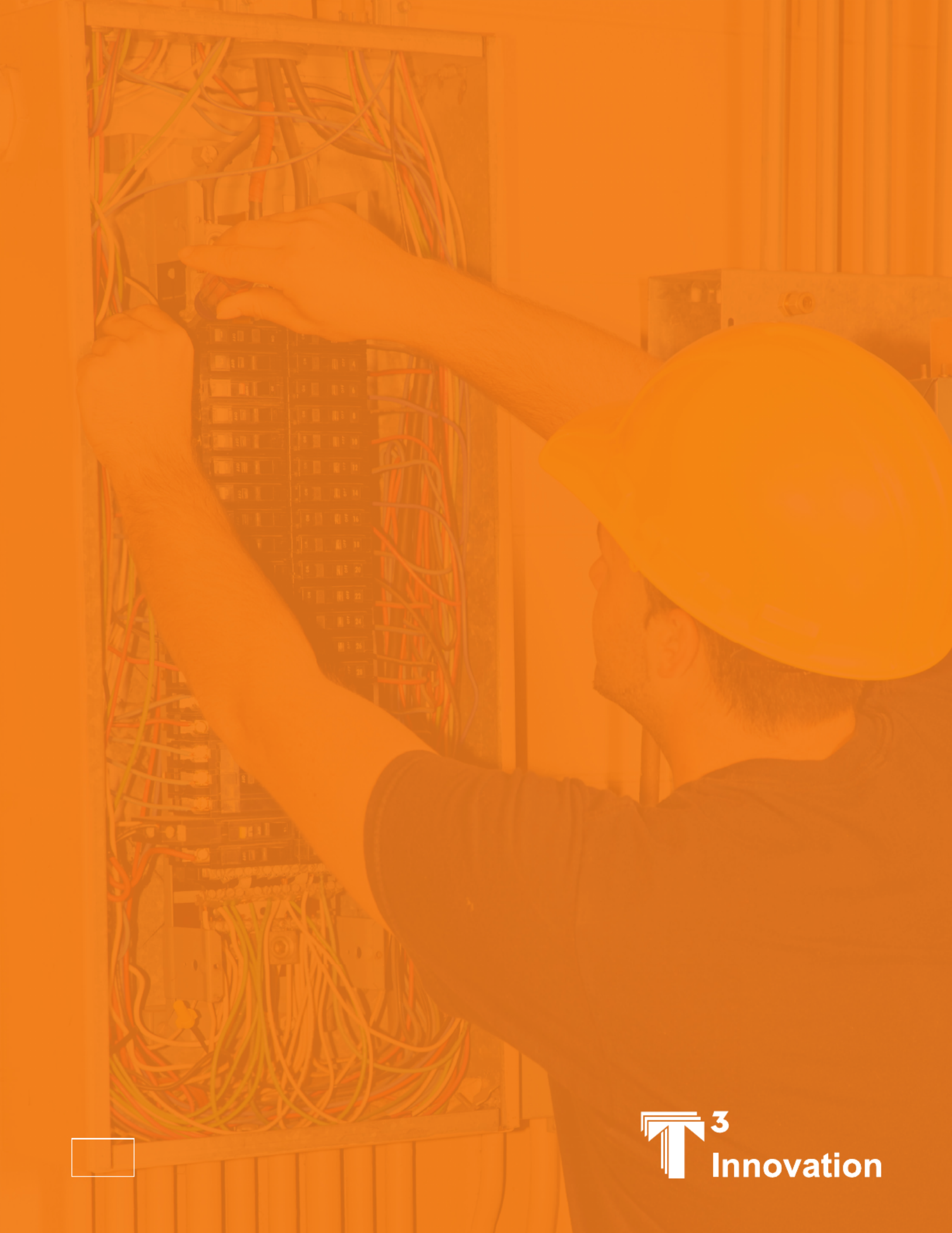
Whitepaper: Spread Spectrum Time-Domain Refl ectometry www.T3Innovation.com
SPREAD-SPECTRUM
TIME-DOMAIN
REFLECTOMETRY
SSTDR
WHITEPAPER:
MADE IN
USA
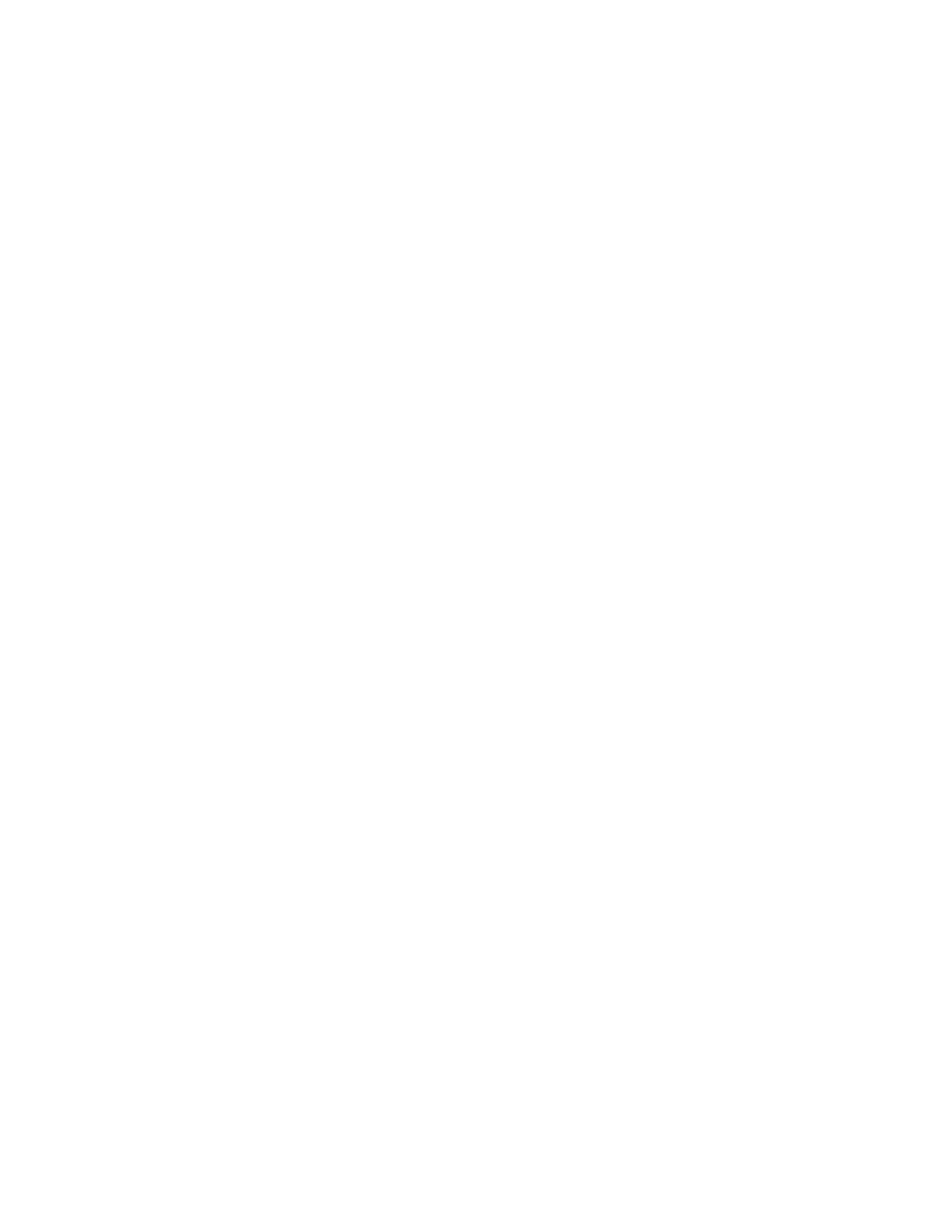
Whitepaper: Spread Spectrum Time-Domain Reectometry www.T3Innovation.com
IEEE SENSORS JOURNAL, VOL. 5, NO. 6, DECEMBER 2005 1469
Analysis of Spread Spectrum Time Domain
Reflectometry for Wire Fault Location
Paul Smith, Member, IEEE , Senior Member, IEEE , Member, IEEE, Cynthia Furse , and Jacob Gunther
Abstract—Spread spectrum time domain reflectometry (SSTDR)
and sequence time domain reflectometry have been demonstrated
to be effective technologies for locating intermittent faults on air-
craft wires carrying typical signals in flight. This paper examines
the parameters that control the accuracy, latency, and signal to
noise ratio for these methods. Both test methods are shown to be
effective for wires carrying ACpower signals, and SSTDR is shown
to be particularly effective at testing wires carrying digital sig-
nals such as Mil-Std 1553 data. Results are demonstrated for both
controlled and uncontrolled impedance cables. The low test signal
levels and high noise immunity of these test methods make them
well suited to test for intermittent wiring failures such as open cir-
cuits, short circuits, and arcs on cables in aircraft in flight.
Index Terms—Aging wire detection, arc detection, sequence time
domain reflectometry (STDR), spread spectrum time domain re-
flectometry (SSTDR), time domain reflectometry (TDR), wire fault
detection.
I. INTRODUCTION
FOR MANY years, wiring has been treated as a system that
could be installed and expected to work for the life of an
aircraft [1]. As aircraft age far beyond their original expected
life span, this attitude is rapidly changing. Aircraft wiring prob-
lems have recently been identified as the likely cause of several
tragic mishaps [2] and hundreds of thousands of lost mission
hours [3]. Modern commercial aircraft typically have more than
100 km of wire [2]. Much of this wire is routed behind panels or
wrapped in special protective jackets, and is not accessible even
during heavy maintenance when most of the panels are removed.
Among the most difficult wiring problems to resolve are those
that involve intermittent faults [4]. Vibration that causes wires
with breached insulation to touch each other or the airframe,
pins, splices, or corroded connections to pull loose, or “wet
arc faults” where water drips on wires with breached insulation
causing intermittent line loads. Once on the ground these faults
Manuscript received April 10, 2004; revised September 14, 2004. This work
was supported in part by the Utah Center of Excellence for Smart Sensors and in
part by the National Science Foundation under Contract 0097490. The associate
editor coordinating the review of this paper and approving it for publication was
Prof. Michael Pishko.
P. Smith is with VP Technology, LiveWire Test Labs., Inc., Salt Lake City,
UT 84117 USA (e-mail: psmith@livewiretest.com).
C. Furse is with the Department of Electrical and Computer Engineering, Uni-
versity of Utah, Salt Lake City, UT 84112 USA, and also with VP Technology,
LiveWire Test Labs., Inc., Salt Lake City, UT 84117 USA (e-mail: cfurse@
ece.utah.edu).
J. Gunther is with the Department of Electrical and Computer Engineering,
Utah State University, Logan, UT 84322-4120 USA (e-mail: jake@ece.usu.
edu).
Digital Object Identifier 10.1109/JSEN.2005.858964
often cannot be replicated or located. During the few millisec-
onds it is active, the intermittent fault is a significant impedance
mismatch that can be detected, rather than the tiny mismatch
observed when it is inactive. A wire testing method that could
test the wires continually, including while the plane is in flight
would, therefore, have a tremendous advantage over conven-
tional static test methods.
Another important reason to test wires that are live and in
flight is to enable arc fault circuit breaker technology [5] that is
being developed to reduce the danger of fire due to intermittent
short circuits. Unlike traditional thermal circuit breakers, these
new circuit breakers trip on noise caused by arcs rather than re-
quiring large currents. The problem is that locating the tiny fault
after the breaker has tripped is extremely difficult, perhaps im-
possible. Locating the fault before the breaker trips could enable
maintenance action.
This paper describes and analyzes one such method, based
on spread spectrum communication techniques that can do just
that. This method is accurate to within a few centimeters for
wires carrying 400-Hz aircraft signals as well as MilStd 1553
data bus signals. Results are presented on both controlled and
uncontrolled impedance cables up to 23 m long.
Early research on spread spectrum time domain reflectometry
(SSTDR) [6] has considered fault location tests on high voltage
power wires. Sequence time domain reflectometry (STDR) [7]
has been studied and used to test twisted pairs for use in commu-
nications. More recently, it has been demonstrated for location
of intermittent faults such as those on aircraft wiring [18]. These
test methods could be used as part of a smart wiring system
[2], and could provide continuous testing of wires on aircraft
in flight, with automatic reporting of fault locations to facilitate
quick wiring repairs. This could be done by integrating the elec-
tronics into either the circuit breaker or into “connector savers”
throughout the system. In order for this to be feasible, the pro-
totype system that has been described here is being redesigned
as a custom ASIC, which should cost on the order of $10–$20
per unit in bulk. This paper focuses on the analysis of SSTDR
and STDR. Parameters required for these methods to function
as potential test methods on wires carrying 400-Hz ACor high
speed digital data such as Mil-Std 1553 are discussed. This anal-
ysis is critical to determine the system tradeoffs between speed,
accuracy, code length/system complexity, etc. This ideal anal-
ysis provides information on the expected accuracy, which is
verified with tests of near-ideal lossless controlled impedance
coax. The effect of realistic noncontrolled impedance cable is
also evaluated, and sources of error within a realistic system are
discussed.
1530-437X/$20.00 © 2005 IEEE
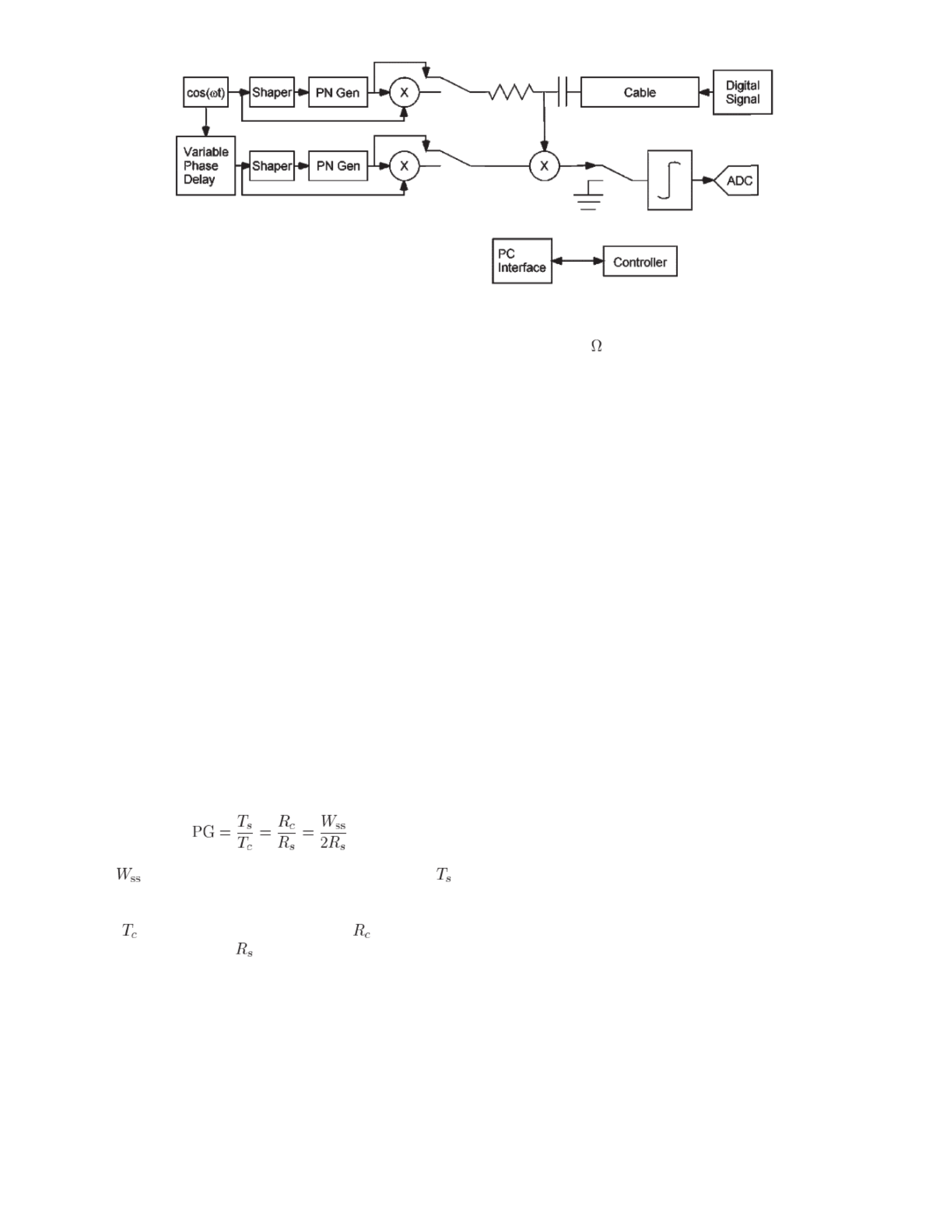
Whitepaper: Spread Spectrum Time-Domain Reectometry www.T3Innovation.com
1470 IEEE SENSORS JOURNAL, VOL. 5, NO. 6, DECEMBER 2005
Fig. 1. S/SSTDR circuit diagram.
II. CURRENT WIRE T TEST ECHNOLOGY
There are several test technologies that can be used to pin-
point the location of wiring faults. Some of the most publicized
methods are: time domain re ectometry (TDR) [8], standingfl
wave refl flectometry (SWR) [12], frequency domain re ectom-
etry (FDR) [13], impedance spectroscopy [14], high voltage,
inert gas [15], resistance measurements, and capacitance mea-
surements. At the present time, these test methods cannot re-
liably distinguish small faults such as intermittent failures on
noncontrolled impedance cables without the use of high voltage.
In addition, the signal levels required to reliably perform these
tests may interfere with aircraft operation if applied while the
aircraft is in use [4]. Another test method is needed that can test
in the noisy environment of aircraft wiring, and that can be used
to pinpoint the location of intermittent faults such as momentary
open circuits, short circuits, and arcs.
III. SPREAD PECTRUM IRE ESTINGS W T
Spread spectrum signals, both in baseband (STDR) [7] and
modulated (SSTDR) [6], are detectable through cross correla-
tion, even though they may be buried in noise. The ability to
pick out the signal is due to processing gain, which for direct
sequence spread spectrum (DSSS) can be expressed as
where is the bandwidth of the spread-spectrum signal, is
the duration of one entire STDR/SSTDR sequence (considering
the entire sequence equal to one bit in communication-system
terms), is the duration of a PN code chip, is the chip rate
in chips per second, and is the symbol rate, which in this
case is the number of full sequences per second [16].
Because of this processing gain, it is reasonable to assume
that a spread spectrum test system could operate correctly in a
noisy environment with 400-Hz 115-V ACor digital data on the
wires. The test system could be designed such that it would not
be damaged by or interfere with any of the signals already on
the wires. For the analysis that follows, the digital data on the
wires will be assumed to be Mil-Std 1553, a standard aircraft
communication data bus that speci es a 1 Mbit/second data rate,fi
a 2.25 20 V RMS signal level, normally operates on low-loss–
(3 dB/100 m) 70- shielded twisted pair cable, and allows for a
SNR of 17.5 dB [17].
The block diagram of the STDR/SSTDR block is shown in
Fig. 1. A sine wave generator (operating at 30 100 MHz) creates–
the master system clock. Its output is converted to a square wave
via a shaper, and the resulting square wave drives a pseudo-noise
digital sequence generator (PN Gen). To use SSTDR, the sine
wave is multiplied by the output of the PN generator, generating
a DSSS binary phase shift keyed (BPSK) signal. To use STDR,
the output of the PN generator is not mixed with the sine wave.
The test signal is injected into the cable. The total signal from
the cable (including any digital data or ACsignals on the cable,
and any re ections observable at the receiver) is fed into a cor-fl
relator circuit along with a reference signal. The received signal
and the reference signal are multiplied, and the result is fed to
an integrator. The output of the integrator is sampled with an
analog-to-digital converter (ADC). A full correlation can be col-
lected by repeatedly adjusting the phase offset between the two
signal branches and sampling the correlator output. The loca-
tion of the various peaks in the full correlation indicates the lo-
cation of impedance discontinuities such as open circuits, short
circuits, and arcs (intermittent shorts). Test data indicate that this
test method can resolve faults in a noisy environment to within
1/10th to 1/100th the length of a PN code chip on the cable, de-
pending on the noise level, cable length, and type of cable [4].
IV. STDR/SSTDR ANALYSIS
The operation of STDR/SSTDR depends on the fact that por-
tions of electrical signals are re ected at discontinuities in thefl
characteristic impedance of the cable. A spread spectrum signal
shown in Fig. 2 is injected onto the wires, and as with TDR,
the re ected signal will be inverted for a short circuit and willfl
be right-side-up for an open circuit [8]. The observed re ectedfl
signal is correlated with a copy of the injected signal. The shape
of the correlation peaks is shown in Fig. 3. In this gure, thefi
modulating frequency is the same as the chip rate. Note that the
sidelobes in the correlation peak are sinusoids of the same am-
plitude as the off-peak autocorrelation of the ML code. This is
due to the selected modulation frequency and synchronization.
Use of a different modulation frequency or different synchro-
nization will yield a different correlation pattern that may have
higher side lobes [4]. Different PN sequences also have different
peak shapes, as shown in Fig. 4 for ML and gold codes.
Product specificaties
Merk: | Platinum |
Categorie: | Kabels voor pc's en randapparatuur |
Model: | TSS200 |
Kleur van het product: | Black, Orange |
Gewicht: | 340 g |
Ondersteund aantal accu's/batterijen: | 4 |
Temperatuur bij opslag: | -20 - 60 °C |
Afmetingen (B x D x H): | 80 x 33 x 173 mm |
Bedrijfstemperatuur (T-T): | 0 - 50 °C |
Relatieve vochtigheid in bedrijf (V-V): | 10 - 90 procent |
Type beeldscherm: | LCD |
Heb je hulp nodig?
Als je hulp nodig hebt met Platinum TSS200 stel dan hieronder een vraag en andere gebruikers zullen je antwoorden
Handleiding Kabels voor pc's en randapparatuur Platinum
30 Mei 2023
25 Mei 2023
22 Mei 2023
Handleiding Kabels voor pc's en randapparatuur
- AMX
- Gefen
- Inno-Hit
- Marmitek
- Extron
- ICC
- ACV
- ESI
- Gofanco
- J-Tech Digital
- Leviton
- Kurth Electronic
- Vantage Point
- ASSMANN Electronic
- Audiovox
Nieuwste handleidingen voor Kabels voor pc's en randapparatuur
5 Augustus 2025
5 Augustus 2025
5 Augustus 2025
4 Augustus 2025
29 Juli 2025
29 Juli 2025
28 Juli 2025
26 Juli 2025
25 Juli 2025
21 Juli 2025