Little Giant W16G07S8-32P Handleiding
Little Giant
Pomp
W16G07S8-32P
Bekijk gratis de handleiding van Little Giant W16G07S8-32P (24 pagina’s), behorend tot de categorie Pomp. Deze gids werd als nuttig beoordeeld door 85 mensen en kreeg gemiddeld 4.4 sterren uit 43 reviews. Heb je een vraag over Little Giant W16G07S8-32P of wil je andere gebruikers van dit product iets vragen? Stel een vraag
Pagina 1/24
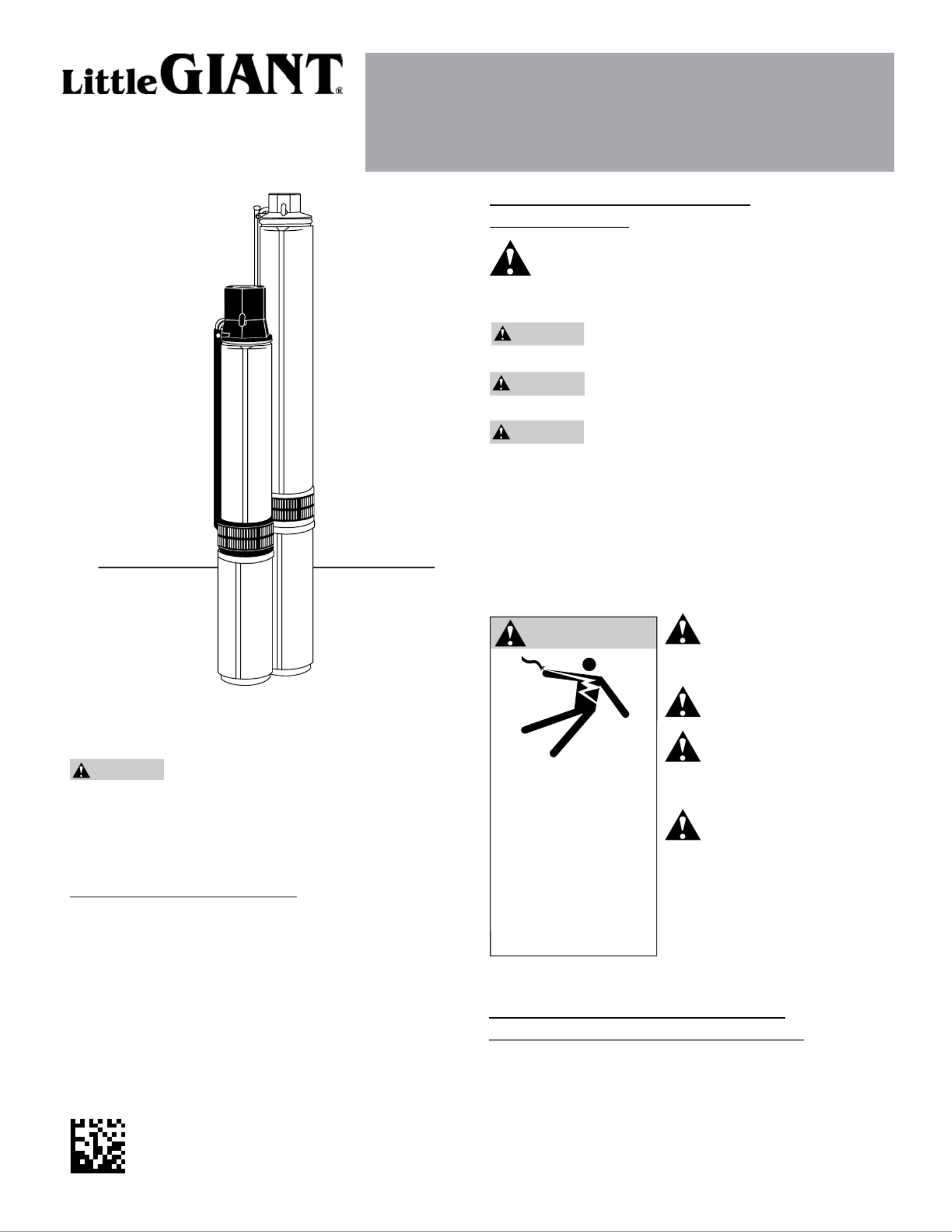
OWNER’S MANUAL
4” SUBMERSIBLE PUMP
BEFORE INSTALLING PUMP, BE SURE TO READ
THIS OWNER’S MANUAL CAREFULLY.
Fill the pump with water before starting or
the pump will be damaged. The motor on this pump is
guaranteed by the manufacturer, and in the event of failure
it must be returned to an authorized service station for
repairs. The motor warranty is void if repairs are not made
by an authorized repair station.
INSPECT THE SHIPMENT
Examine the pump when it is received to be sure there
has been no damage in shipping. Should any be evident,
report it immediately to the dealer from whom the pump
was purchased. Please check the pump package to see
that it includes pump, motor, and motor leads (if your pump
purchase includes a motor).
This pump includes either a built-in or externally-mounted
check valve with the discharge head. Make certain that your
available voltage corresponds to that of your motor.
C A U T I O N
READ AND FOLLOW SAFETY
INSTRUCTIONS
This is the safety alert symbol. When you see this
symbol on your pump or in this manual, look for one of
the following signal words and be alert to the potential for
personal injury:
D A N G E R
warns about hazards that cause serious will
personal injury, death, or major property damage if ignored.
WARNING
warns about hazards that cause serious can
personal injury, death, or major property damage if ignored.
C A U T I O N
warns about hazards that or cause will can
minor personal injury or major property damage if ignored.
The label indicates special instructions, which are NOTICE
important but not related to hazards.
Carefully read and follow all safety instructions in this
manual and on pump.
Keep safety labels in good condition.
Replace missing or damaged safety labels.
Wire motor for correct
voltage. See Electrical
Information section of this manual
and motor nameplate.
Ground motor before
connecting to power supply.
Meet National Electrical
Code, Canadian Electrical
Code, and local codes for all
wiring.
Follow wiring instructions in
this manual when
connecting motor to power lines.
Hazardous voltage.
Can shock, burn, or
cause death.
Ground pump before
connecting to power
supply. Disconnect
power before working
on pump, motor
or tank.
WA R N I N G
Franklin Electric Co., Inc.
www.franklinwater.com
customerservice@lgpc.com
ATTENTION!
IMPORTANT INFORMATION FOR
INSTALLERS OF THIS EQUIPMENT!
THIS EQUIPMENT IS INTENDED FOR INSTALLATION BY
TECHNICALLY-QUALIFIED PERSONNEL. FAILURE TO
INSTALL IT IN COMPLIANCE WITH NATIONAL AND LOCAL
ELECTRICAL CODES AND WITH FRANKLIN ELECTRIC
RECOMMENDATIONS MAY RESULT IN ELECTRICAL SHOCK
OR FIRE HAZARD, UNSATISFACTORY PERFORMANCE,
Form 106257101 Rev. 002 11/2013
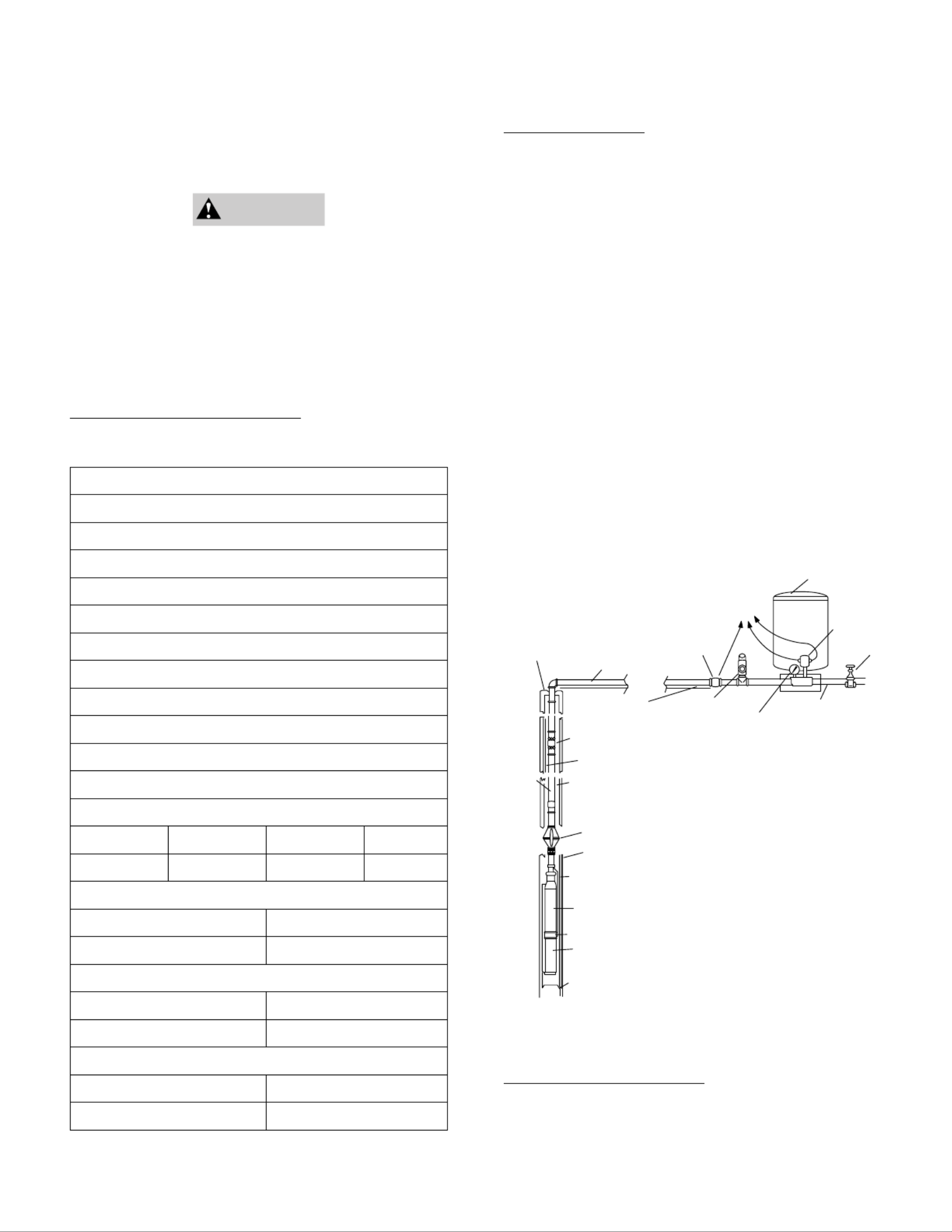
2
AND EQUIPMENT FAILURE. FRANKLIN ELECTRIC
INSTALLATION INFORMATION IS AVAILABLE FROM PUMP
MANUFACTURERS AND DISTRIBUTORS, AND DIRECTLY
FROM FRANKLIN ELECTRIC. CALL FRANKLIN ELECTRIC
TOLL FREE AT 800-701-7894 FOR INFORMATION. RETAIN
THIS INFORMATION SHEET WITH THE EQUIPMENT FOR
FUTURE REFERENCE.
W A R N I N G
SERIOUS OR FATAL ELECTRICAL SHOCK MAY RESULT
FROM FAILURE TO CONNECT THE MOTOR, CONTROL
ENCLOSURES, METAL PLUMBING, AND ALL OTHER
METAL NEAR THE MOTOR OR CABLE TO THE POWER
SUPPLY GROUND TERMINAL USING WIRE NO SMALLER
THAN MOTOR CABLE WIRES. TO REDUCE RISK OF
ELECTRICAL SHOCK, DISCONNECT POWER BEFORE
WORKING ON OR AROUND THE WATER SYSTEM. DO
NOT USE MOTOR IN SWIMMING AREAS.
INSTALLATION RECORDS
It is a good idea to keep an accurate record of your
installation. Be sure to record the data below:
Purchased from:
Date of installation:
Pump model*:
Pump date code*:
Well inside diameter (in/mm):
Depth of well (ft/m):
Depth of water (ft/m):
Pump setting (ft/m):
Drop pipe size:
Wire size (pump to control box):
Wire size (control box to power source):
Horizontal offset (between well & house):
Make of motor*
Amps HP Volts Phase
Make of control box
HP Volts
Power supply
Volts HZ
Pressure switch limits
Cut-in (PSI) Cut-out (PSI)
*This information is on your pump or motor tag. It will help
us identify your pump in case of later inquiries.
TEST RUNNING
If test running pump before installation:
1. Ensure that the power supply corresponds with that
shown on the nameplate of the motor and control box (if
required).
2. Install pump and components appropriate for the test as
shown in Fig. 1.
3. Make sure power supply is turned off and circuit
breaker or disconnect switch is open. Make electrical
connections appropriate to your motor as shown in
Figure 2, 3 or 4.
4. On a three-phase motor, use a magnetic starter equipped
with quick-trip, ambient compensated heaters of correct
size for the horsepower of the motor.
To ensure correct rotation of three-phase units, brace
pump shell securely and apply power momentarily by
snapping line switch quickly on and off. If rotation is
correct, reaction of the shell will be clockwise when
viewed from pump discharge (that is, pump shaft will
rotate counter clockwise). Interchange any two leads at
magnetic starter to reverse rotation.
5. Run pump and motor unit for a few seconds to ensure
that it is in working order.
FIGURE 1
Installation Diagram
Pressure tank
Pressure switch
Gate valv
Service pipe
Pressure gauge
Pressure relief valve
Spring-loaded
check valve
See Wiring Diagrams
Sanitary well seal
or pitless adapter Discharge pipe
Submersible cable
Spring-loaded
check valve
(Recommended every 100’/30m)
Safety cable
Drop pipe
Cable
(secured to drop
pipe with tape or
clamps every 10’/3m)
Well casing
Spring-loaded
check valve
at pump discharge
Submersible
pump
Suction screen
Motor
Well screen or
casing perforations
Note: Keep pump at least 5' (1.5 m) from
bottom of well and above well screen
or casing perforations.
Torque arrestor
SUITABILITY OF WELL
Install the pump only in a well that has been properly
developed. Water from an undeveloped well often contains
an excessive amount of sand, dirt, and abrasives which can
damage the pump. Check that the well is large enough to
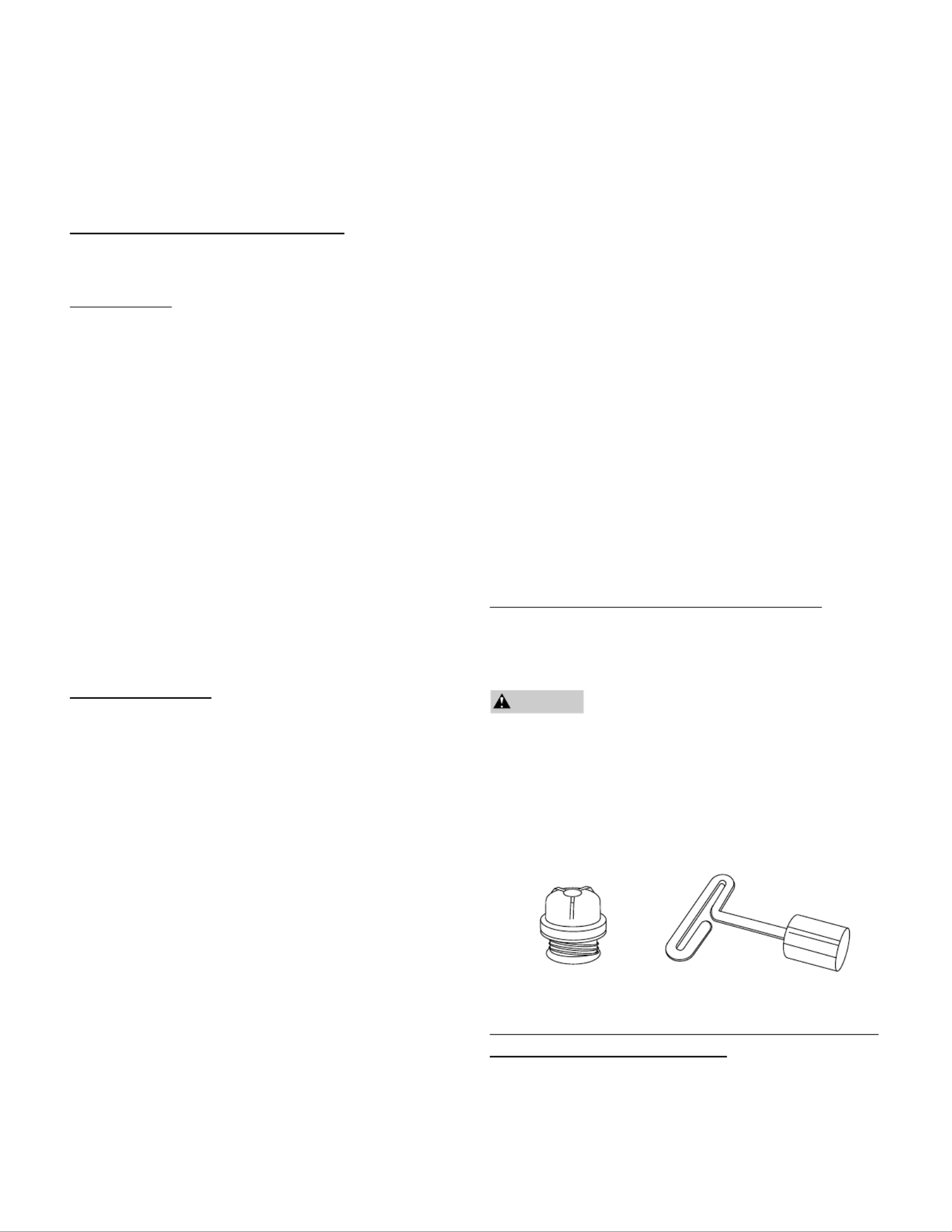
3
allow the pump to be set at the required depth. Do not set the
pump below the casing perforations or well screen unless you
make arrangements to ensure an adequate ow of water over
the motor for cooling purposes. Determine the correct pump
setting from the driller’s record by taking into account the
static water level and the drawdown at the proposed pumping
rate. Keep the pump at least ve feet from the bottom of a
drilled well.
SPLICING THE POWER CABLE
Follow the instructions enclosed in the cable splicing kit
(purchased separately).
DROP PIPE
Submersible drop pipe manufacturer’s usage guidelines
should always be followed when suspending a submersible
pump in a well. Generally either galvanized steel or plastic are
used for the pump drop pipe. When using plastic piping it is
important to follow the manufacturer’s depth and pressure
rating. Give special consideration to:
1. A safety cable to prevent loss of pump if pipe should break.
2. A torque arrestor just above pump to prevent chang the
cable when pump and pipe twist during the starting and
stopping cycle. (See Figure 1.)
Schedule 40 galvanized pipe is suitable for settings to 600
feet (180m). For deeper settings, use schedule 40 pipe for the
bottom 600 feet (180m), and schedule 80 for the remainder.
NOTICE: Drop pipe sizes and usages depths should be
considered as general guidelines only. Drop pipe manufacturer
data and recommendations supersedes these instructions.
Take great care to keep pipes clean and free from pebbles,
scale, and thread chips. Make sound, air-tight connections at
all ttings. Pipe sealant is recommended.
CHECK VALVES
It is recommended that one or more check valves always be
used in submersible pump installations. If the pump does not
have a built-in check valve, an inline check valve should be
installed in the discharge line within 25 feet of the pump and
below the draw down level of the water supply. If permitted by
local codes it is recommended that an additional check valve
be installed in the system plumbing between the wellhead
and the system’s pressure tank. For pump installations that
are more than 200 feet (60m) below the wellhead; additional
check valves should be installed in the drop pipe. This should
be done at intervals of 200 feet (60m) or at the check valve
manufacturer’s specied installation interval. More than one
check valve is often needed, but more than the recommended
number of check valves should not be used.
Swing type check valves are not acceptable and should never
be used with submersible motors/pumps. Swing type check
valves have a slower reaction time which can cause water
hammer (see next page). Internal pump check valves or spring
loaded check valves close quickly and help eliminate water
hammer.
Check valves are used to hold pressure in the system when
the pump stops. They also prevent backspin, water hammer
and upthrust. Any of these can lead to early pump or motor
failure.
NOTE: Only positive sealing check valves should be used in
submersible installations. Although drilling the check valve or
using drain-back check valves may prevent back spinning,
they create upthrust and water hammer problems.
A. Backspin - With no check valve or a failed check valve,
the water in the drop pipe and the water in the system can
ow down the discharge pipe when the motor stops. This can
cause the pump to rotate in a reverse direction. If the motor is
started while it is back spinning, an excessive force is placed
across the pump-motor assembly that can cause impeller
damage, motor or pump shaft breakage, excessive bearing
wear, etc.
B. Upthrust - With no check valve, a leaking check valve, or
drilled check valve, the unit starts under a zero head condition.
This causes an uplifting or upthrust on the impeller-shaft
assembly in the pump. This upward movement carries across
the pump-motor coupling and creates an upthrust condition in
the motor. Repeated upthrust can cause premature failure of
both the pump and the motor.
C. Water Hammer - If the lowest check valve is more than 30
feet above the standing (lowest static) water level, or a lower
check valve leaks and the check valve above holds, a vacuum
is created in the discharge piping. On the next pump start,
water moving at very high velocity lls the void and strikes the
closed check valve and the stationary water in the pipe above
it, causing a hydraulic shock. This shock can split pipes, break
joints and damage the pump and/or motor. Water hammer can
often be heard or felt. When discovered, the system should
be shut down and the pump installer contacted to correct the
problem.
REMOVABLE POPPET CHECK VALVE
4” submersible pumps with a 1-1/4” discharge are supplied
with a spring-loaded, removable poppet check valve
assembly. This check valve can be removed from the pump
discharge when drain back is desired.
WARNING
Fluid draining back through the pump can
cause the pump to rotate backwards. If pump/motor starts
during this time, damage to the pump can occur.
The check valve can be removed using a T-handle poppet
wrench (purchased separately), or with standard needle-nosed
pliers. The poppet assembly is left-hand threaded and is
removed by turning clockwise.
When reinstalling a poppet check valve assembly, tighten it to
15 inch-pounds.
Poppet Assembly T-Handle Poppet Wrench
INSTALLATION OF PUMP, DROP PIPE, AND
ASSOCIATED EQUIPMENT
Figure 1 illustrates a typical well installation showing in ground
components. Adhere to the following items when installing the
pump and drop pipe:
1. Fasten the submersible cable to the drop pipe with clamps
or appropriate tape every 10 ft. (3m) to prevent tangling and
Product specificaties
Merk: | Little Giant |
Categorie: | Pomp |
Model: | W16G07S8-32P |
Heb je hulp nodig?
Als je hulp nodig hebt met Little Giant W16G07S8-32P stel dan hieronder een vraag en andere gebruikers zullen je antwoorden
Handleiding Pomp Little Giant
31 Maart 2025
31 Maart 2025
31 Maart 2025
4 September 2024
4 September 2024
4 September 2024
4 September 2024
4 September 2024
4 September 2024
4 September 2024
Handleiding Pomp
- Fuxtec
- Dream Power
- Waldbeck
- Jabsco
- Wetelux
- SKS
- Scheppach
- POLARIS
- Melinera
- Milwaukee
- Toolcraft
- Nowax
- ESPA
- SANDPIPER
- Fieldmann
Nieuwste handleidingen voor Pomp
29 Juli 2025
21 Juli 2025
15 Juli 2025
14 Juli 2025
14 Juli 2025
7 Juli 2025
7 Juli 2025
7 Juli 2025
5 Juli 2025
3 Juli 2025